Buyer’s Guide
What to look for in your piano or keyboard
For the average person, shopping for a piano can be a confusing task.
- Why does one piano cost more than another?
- What brand is better?
We hear questions like these every day and we want you to be able to make an educated decision.
By offering you some insight from industry experts, we hope to arm you with the knowledge to ask the right questions before ever visiting the showroom.
Piano Cost
The simple answer is because high quality pianos are more expensive to manufacture than lesser quality instruments.
Selection of Materials
The finest materials—top grade spruce, wool felt, expensive hard rock maple, German steel strings and all the components that go into the making of a piano — will affect the end result. The makers of more expensive instruments take great care in selecting and handling their materials consistent with the quality of that instrument.
Preparation of Materials
Proper seasoning of wood is time-consuming and costly. First the wood must be air-dried for a period of time, and then placed in kilns to stabilize it to specific moisture content. Through this process, better instrument manufacturers go to great lengths to ensure the quality and long life of their pianos.
Workmanship
There is no substitute for quality workmanship. The more skilled the workers are, the better the piano. remember that the better the tools, the better the piano as well. There are some jobs that machines can accomplish better than even the most skilled workman might with years of experience.
Scale Design
A beautifully balanced scale is the result of the work of a master scale designer. Scales tend to evolve and be refined over a period of time. Manufacturers of the finest pianos constantly strive to find ways to make their scale designs even better.
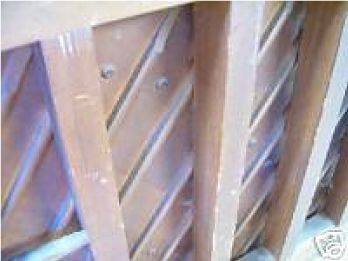
The Back
The back of a vertical piano or the bottom in the case of a grand, is the piano’s foundation, and must be strong and stable to withstand the tons of “pull” exerted by the strings.
Although the strings are mounted on steel, this is the reason for the vertical’s back posts or in a grand, the braces underneath the piano.
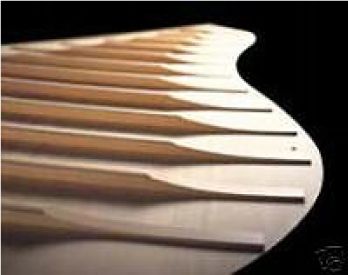
The Soundboard
The soundboard is the heart of the piano. It is one of the most important, yet least understood part of the instrument. Its purpose is to convert the vibrations of the strings into what we hear as a tone. Without it there would be no amplification, and we would hear little if anything. If the soundboard is not made of the proper kind of wood, if its size, thickness, crown (curvature), grain direction, texture and other factors are not in balance, the end result will be unacceptable tone, texture, and sustaining quality.
Spruce is the species of wood that nearly all manufacturers of top-quality pianos use for their soundboards. There are several grades of spruce and the best quality pianos have more grains per inch.
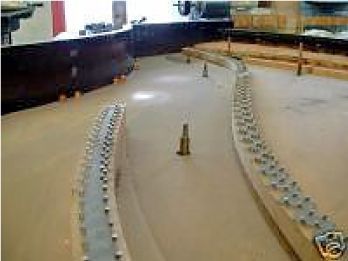
Bridges
A critical step in the making of fine quality piano is the shaping and fitting of the bridges. The bass and treble bridges must be planned to exact thickness from end to end and fitted securely to the soundboard. Absolute accuracy is paramount so as to provide the proper down-bearing of the strings upon the bridges. It is this correct down-bearing which is so vital for the transfer of the string vibrations to the soundboard (resulting in the fine tonal quality from the lowest bass string to the highest treble).

The Pin Block
The pin block is a laminated hardwood plank running the width of the piano and attached to the back frame. Embedded in holes in the pin block are the steel tuning pins around which is coiled one end of a piano string. The pin block has to hold the tuning pins tight enough, by friction alone, so that all the strings are maintained at the correct tension without unwinding —thus keeping the piano in tune.
The durability of its pin block is important to the longevity or “life” of the piano. Defective pin blocks can be replaced on grand pianos (at great expense); however, it is nearly impossible to replace a vertical pianos pin block. Pin blocks come in several different varieties, which differ in the number of laminations they contain (from four to nearly fifty.) The single most important thing is that the pin block is properly designed and the holes are drilled accurately. Hard rock maple is the material of choice.
Properly designed pin blocks made with well-seasoned woods will often last the life of the piano if kept in proper climactic conditions. Loose pins are usually a result of a poor pin block or excessive dryness over a period of time.
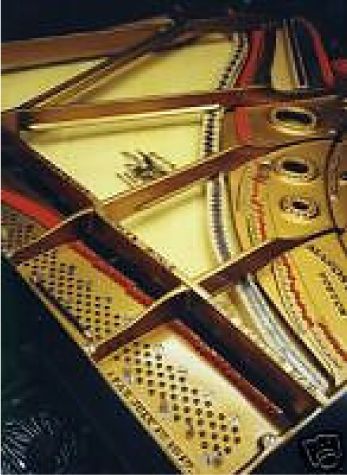
The Piano Plate
The piano plate or harp is made of fine gray cast iron, to the individual manufacturer’s specifications and scale design. The plate along with the back frame to which it is attached, is the foundational strength to resist the tons of string tension placed upon it. The construction of the plate has been greatly refined.

Pedals
Most pianos have three pedals, but occasionally you see some with just two pedals. Today’s two-pedal pianos are usually pianos manufactured and sold outside of the United States.
Grands
The right pedal, called the damper or sustaining pedal, operates on the grand piano just the same as in the vertical piano. It lifts the dampers from the strings and allows all the strings to sound until the pedal is released. This is the pedal that is used most frequently. The left pedal is called the “una corda” pedal. When depressed, the entire action and keyboard is shifted slightly to on side so that the hammers only strike two strings rather than the three strings per note. This slightly changes the character of the sound, as well as makes the piano sound a little softer. The middle pedal on a grand piano function in one of two ways. on some pianos it functions as a bass sustain. On others, the middle pedal is the “sostenuto” pedal. When depressed, it will sustain a single note or individual chord without affecting the rest of the keyboard. While this pedal is almost exclusively found on grands, very high-quality uprights are equipped with a true sostenuto pedal as well.
Verticals
The right pedal is the same as that of a grand piano. The left pedal is the soft pedal. When depressed, it moves all the hammers close to the strings so the stroke is shortened, resulting in a softer sound. The middle pedal on a vertical piano is often a bass sustaining pedal. When depressed it lifts off the dampers in the bass section. On some vertical pianos the middle pedal is a “practice” pedal or “muting” pedal. When it is depressed, a thin strip of felt is lowered between the hammer and the strings, which muffles the sound to a very low level.
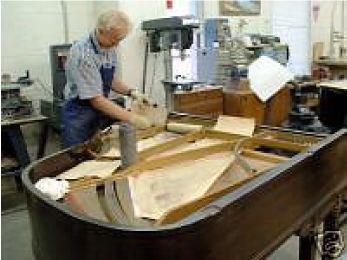
Scale Design
Piano construction begins with the scale design. Reduced to simple terms, the scale is the physical layout of the strings and other components which produce or affect the sound and tone quality of the piano. The scale designer must consider the speaking length of the string, the gauge, or wire size of each string, the tension, in pounds to which each string is drawn when it is tuned to exact pitch and the gauge of the pure copper winding of the bass strings. All of the factors are interdependent. One cannot be changed without affecting all of the others. Differences in scale design give different pianos their own special tonal qualities or personalities.
If all of these factors are in proper relationship to one another, we have harmony, and the result is an excellent foundation upon which a quality piano may be built. Scale designers are the tonal architects of the piano.
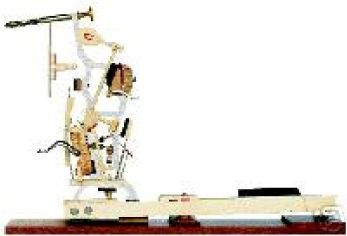
Keys and Action
Each key is mounted on a key frame. Key frames are located in exact position by center pins which are at the balance point of the key. Quality pianos have weighted and balanced keys for consistency of touch and weight throughout the entire range of the keyboard. Ivory has not been used for the key tops for over 70 years. Today piano manufacturers use more modern composition materials, which give the keys their appearance and durability required. The white keys will never yellow, nor will they crack, split, or chip (Some manufacturer’s technical expertise allows them to use materials that nearly duplicate ivory’s ability to absorb moisture and remain soft and warm to the touch).
Now let’s discuss the action—the business end of the piano. This section of the piano consists of nearly 1500 parts and causes the hammer to strike the strings when the keys are struck. Most parts of a piano are traditionally made of hard northern maple or modern composite materials. In addition, several kinds of pure wool felt and bushing cloth, leather, steel, brass, nickel, glue, plus many hours of work go into the making of today's piano action.
“Strike the key and the hammer strikes the string” is a greatly over-simplified description of what goes on in a piano action. The hammer not only must strike the string almost instantaneously, it must also strike at an exact point on each string. It must strike with the exact amount of force required to produce volume ranging from pianissimo (very, very soft) to fortissimo (very, very loud), and then bring the hammer back into position, ready to repeat the process over and over at a very rapid rate. The action must also provide damping of the strings, as well as allow the tone to be sustained as long as the key is held down. There can be no lost motion in the action which would spoil the touch. It must perform quietly and efficiently, with a minimum of maintenance under adverse conditions, for many years. Piano hammers are made of fine wool felt which is formed around a hardwood hammer molding. Most piano hammers are made of two layers of felt, the outer layer is white–the inner layer may or may not be colored.
To bring out the best in a piano, the hammer is the all-important link. It’s often said that while a good hammer can’t make a poor piano sound good, a bad hammer can spoil the sound of the best piano. That’s why it is so important that the hammer be properly sized and voiced for the scale of that particular piano.
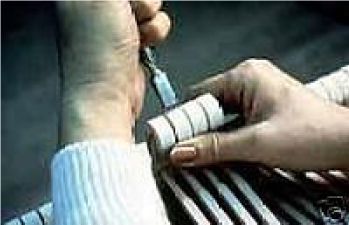
Action Regulation and Voicing
This is the final stage of the manufacturing of a piano. Piano hammers, in spite of being made from the best wool obtainable, and produced under exacting control will vary slightly in density and hardness. This variance is corrected by the use of fine steel needles inserted into the hammers at the proper place and the proper depth. By “needling” a piano hammer, the tone regulator can make the tone of an individual note sound hard, mellow, full or thin. This fine adjustment is called voicing. The end result is tonal balance and an instrument with a full rich tone.
Action regulation is done by skilled technicians at the factory and consists of minute adjustments throughout all the critical points in the action to ensure that each and every key and action assembly performs exactly as it is designed to do to ensure evenness throughout the full range of the keyboard. The finest piano manufacturers spend a great deal of time and attention to this process with their skilled regulators and voicers. Manufacturers of lesser quality pianos spend very little time in the voicing and regulating process. Final preparation of the piano before it leaves the factory is one of the many differences between pianos of differing quality. In the factory, final preparation of the piano includes such things as several tunings, action regulation, and voicing. And finally, before delivery, preparation by the dealer's technicians of the instrument should be done to ensure that the piano is at its very best when it arrives at your home.
Cabinetry
Approximately 85% of every acoustic piano is made of wood and a good portion of that wood is the piano cabinetry. Exquisite furniture and finishes have long been associated with the fine art of piano building. For most piano buyers, the style of cabinetry and wood finish is an important consideration. From period styles to contemporary, there is sure to be a finish and style that will work with your individual decorating tastes.
Historically, piano cabinets have used the solid core construction, and some still do today. However, plywood and fiberboard are no commonly used throughout the industry. Legs, molding, and various trim pieces are usually solid wood. On good quality pianos they are of the same wood species as the rest of the piano's cabinet. While elaborate cabinets with carvings, molding and rich styling features are more expensive than simple plain cabinets, within the same brand and model there is no difference in the quality of the instrument. Proper seasoning of the woods used and the application of a long-lasting finish will ensure the beauty and stability of the cabinet for its many years of service.